第35回:シリーズ『スマートな工場管理へのステップ』(1/2)
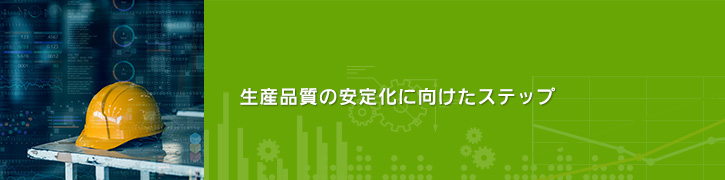
本シリーズでは、『スマートに管理された工場』を一つのゴールとして、その実現に向けた現実的なステップについて考察しています。今回は、スマートに管理された工場の前段階となる「工場全体を俯瞰しながら、ものづくり全体の品質管理」を実現する方法についてご紹介します。
“スマートに管理された工場”の直前ステップ
前回は、古いレトロな設備をIoTデバイス化し、設備データを見える化するソリューション「MP-Viewer」について詳しく説明しました。
MP-Viewerは、レトロな既存設備を、それ自体に手を加えることなく“つながる設備”へと変え、データの収集・可視化を実現するソリューションです(図1)。

このMP-Viewerの活用によって、生産設備がレトロであっても、生産現場の設備データを自動的に収集して、リアルタイムに分析できる環境が構築できます。
このようにして特定生産現場のデータ分析の環境を整えたのちには、その環境を他の工程(別ライン)へ横展開していき、工場内の全ての生産現場の集中管理と一括コントロールを始動させます。それが、本シリーズで追求している『スマートに管理された工場』に向けた第2のステップと言えます。
そして今回お話しするのは、この第2ステップの次の段階(=第3ステップ)である以下のステップです。
工場全体を俯瞰しながら、ものづくり全体の品質管理に取り組む。
このステップを別の言い方で具体的に表現すると、「異なる工程の連携によって『原料-中間材-製品』という一連のデータを管理し、在庫・品質の安定管理を目指す」ということになります。この第3のステップを踏むことで、MES(製造実行システム)とERP(基幹系情報システム)や予兆管理システムなどが連携した『スマートに管理された工場』にまた一歩近づくことになります(図2)。

『原料-中間材-製品』の一連管理で目指すこと
ここからお話しする第3のステップは、「製品」から「原料」へと遡(さかのぼ)るためのトレーサビリティを確保する取り組みと言えます。また、この取り組みの目的は「(製品)品質の安定化」と、製品不良発生時の「原因追求」の2つに大別できます。
このうち、「品質の安定化」は、「ロット間の品質データの比較」と「品質異常発生時の迅速な検知」によって実現され、一方の「原因追求」は、製品を構成する原料と生産設備の情報から問題原因を解明することを指しています。
さらに、これら「品質の安定化」と「原因追求」の2つを可能にするためには、品質データを「原料-中間材─製品」の流れの中で紐づけて管理したり、品質データと生産設備データを連携させながら管理したりする必要があります。
では、こうした品質データ/生産設備データの管理はどのようにして行えばよいのでしょうか。以下、その方法について見ていくことにします。